FURNACES FOR BRAZING

For high quality brazing, short times at brazing temperature, uniform heating and cooling are essential.
For materials like stainless steel, high atmosphere purity is an additional requirement. It is for these reasons that continuous brazing furnaces are a preferred choice.
Fluidtherm Continuous Brazing features include-
​​
-
straight through and humpback designs that significantly reduce the consumption of gas and operating costs
-
excellent temperature uniformity and atmosphere integrity
-
consistently low dew points
-
high process reliability
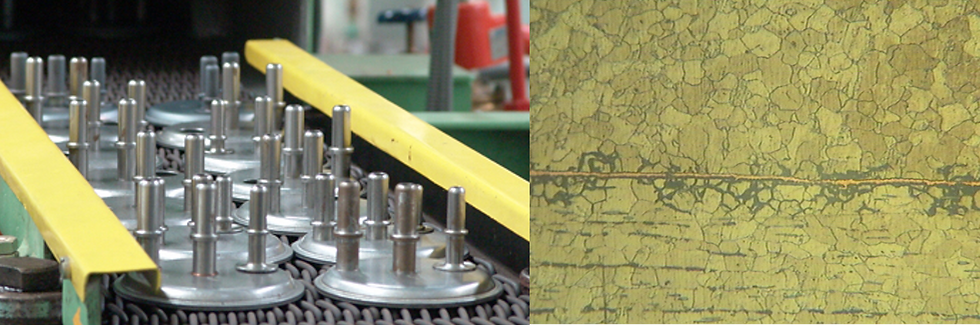
Humpback design reduces wastage of gas

Brake pad brazing to steel plate. Microstructure shows uniform brazing.
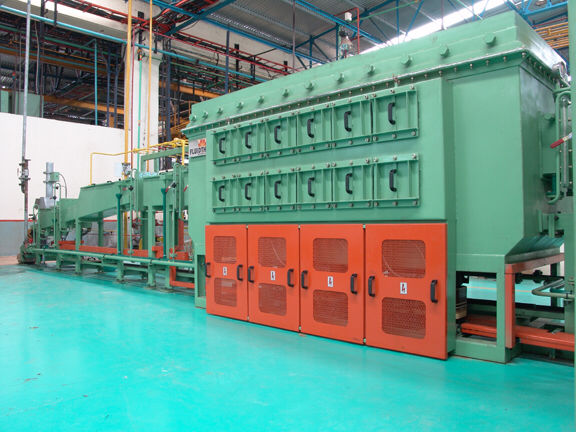
Sinter- Braze Hardening of PM CAM with steel tube
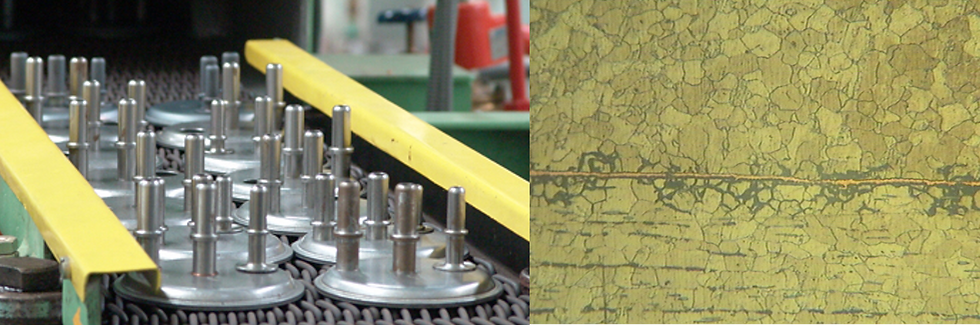
Humpback design reduces wastage of gas
Brazing
Brazing has three distinct characteristics.
-
Joining or uniting of an assembly of two or more parts into one structure; is achieved by heating the assembly or region of the part to the joined to a temperature of 450 °C (842 °F) or above.
-
Assembled parts and brazing filler metal are heated to a temperature high enough to melt the filler metal and not the parts.
-
The molten filler metal spreads into the joint wet the base metal surfaces by capillary action and anchors the parts.
Commonly used brazing methods are
-
Torch brazing
-
Furnace brazing
-
Induction brazing
-
Dip brazing
-
Resistance brazing
Furnace brazing is extensively used when the parts to be brazed can be assembled with brazing filler metal preplaced near the joint. The preplaced filler metal may be in the form of wire, foil, paste or ring. When the brazing is carried out in reducing atmosphere like N2/H2 or dissociated ammonia, separate fluxes are not required in the joint or with filler metal.